From the 1980-81 Bulletin
Tony Peck and John Riding’s start of their circumnavigation, and its halt in the Galapagos islands, has been written up elsewhere.
After abandoning their circumnavigation AKU was passed to a local hotelier who then passed her to his son.
The previous owner, J Anthony Peck, who was too ill to continue his voyage and went to England, signed ‘AKU’ over to my father, who signed it over to me. ‘AKU’ had sat on our beach for a dozen years: that the boat could be saved at all after so many years in a mangrove swamp is testimonial to the excellence of the basic structure. The lichen was 3 inches thick on the topsides and a hole in the bottom admitted high tides and small crabs. Based on the decay I found, I make the following recommendations to Atalanta owners, particularly if your boat is fibreglass sheathed:
- Make as few holes in the GRP as possible. Each little screwhole is inviting rot or worm.
- Especially important on a GRP sheathed boat is not to put any kind of metal skid strips screwed onto the false keel. Far better to make sure the fibreglass is extra thick there. ‘AKU’ had iron strips along the keel and I had to chop off the whole false keel and stem and rebuild with lots of fibreglass . . . . I found that the edges of the plywood hull pieces were neither butted on the centerline of a v bottomed keelson, nor planed flush with the bottom of the keelson. They were left projecting and thefalse keel screwed on to cover the fair-planed edges, leaving a void. If one was built that way, at least a few others must have been
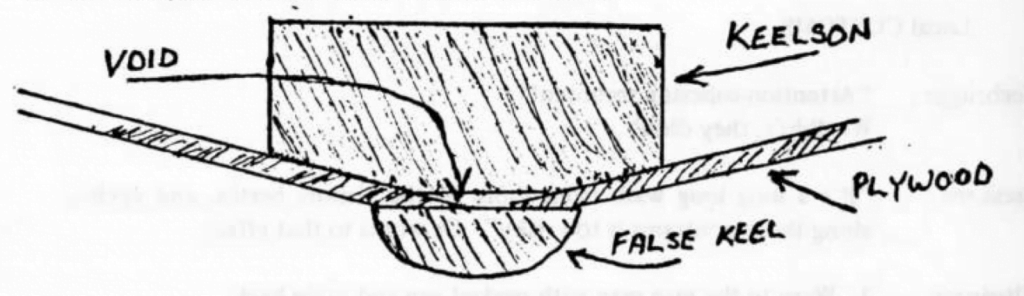
But how to put toe strips on the whale-backed darling without screws? Well, if you can’t give up the aesthetics of a varnished submarine, that’s that. But if your Atalanta is fibreglassed or painted, I can think of several solutions to the slippery deck problem. I don’t like sand or ground walnut shells in the paint as they are both very abrasive to clothing and knees. On other boats I have used fine sawdust patted into the first coat of paint, then swept and vacuumed before subsequent coats. The same treatment might work in the last finish coat of resin in a ‘glas job. Or you could stick a synthetic rope or cord in glass mat with plenty of resin to make a toe rail or anti-skid batten.
Borden ‘Arabol’ – Wonder-paint
My solution is ‘Arabol’. That is probably the best known tradename for a thick white latex based paint-type stickum. Mine was manufactured by Borden and is very good. It will not stick to greasy or oily surfaces and will soften and come off if left in standing water too long. Here’s the whole procedure.
- Brush on a prime coat thinned with a little water.
- Let it cure a few days.
- Wash the sizing out of enough burlap to cover the deck. The dry burlap should then be thoroughly saturated in a pail of Arabol, then squeezed out and applied wet on top of a fresh wet coat of Arabol.
- Your burlap should be precut a little larger than necessary so that you can work quickly and get it all stuck down before it goes tacky. Make sure to get all bubbles out.
- Paint on more Arabol on top of the burlap as you work.
- Judicious stretching and slitting of the burlap will allow you to fit almost any corner or com pound curve. The thoroughly saturated burlap becomes very flexible. Do not use canvas or anything like it as it is not flexible enough and too hard to saturate.
- If the burlap goes too tacky before you get it stuck down, re-saturate it with the brush.
- After you have it all in place, go over everything again and prod the hardening fabric into the corners again to force out any excess Arabol.
- Any areas that don’t look thoroughly saturated should have more Arabol brushed in.
- The idea is to have the fabric completely filled with Arabol, but without any thick puddles between tl1e deck and the fabric. It is easiest to cut off excess fabric with a very sharp knife after it hardens up some, but sometimes while applying it you need to cut the burlap just so for a good fit in a tight spot. Use scissors kept in a pot of water.
- Let the Arabol burlap cure for a day or two, then put on two more daily coats.
- Let it cure four moredays before painting.
I covered the deck, cockpit, and hatches this way and 5 years of equatorial weather have not affected it at all. (We are 45′ south.) I removed all fittings from the deck and gouged out all the rot then plugged all the holes before starting with the Arabol. It goes right down to the rubbing strake. It looks sort of tweedy close up, but it’s a great non-skid non-glare surface and very easy to maintain or patch. Cleanup of tools, brushes, and yourself is with hot water and detergent. One boat came through here that had had Arabol on deck and cabin for 15 years of cruising. The skipper (a real old shellback singlehander) said he had never seen anything better for decks.
Just remembered…
I think Arabol is a type of airconditioning duct lagging cement.
And ‘Burlap’ is the New World version of hessian or sackcloth.